
For some companies, sustainability is no longer simply a buzzword intended to pacify the masses. They’re proactively investing real dollars in real projects to tap into the potential of a new and growing market. In the process, they’re collaborating with other companies, institutions and state agencies to gain a competitive edge even as they lower emissions.
Case in point: Sasol is actively seeking out partners in its sustainability journey through a newly designated “Sustainability Hub” in Lake Charles, promoting its 1,000 acres of “shovel-ready” property as available space for new investments. And in Baton Rouge, ExxonMobil is lobbying to become the site of one of the first advanced recycling plants, which in turn could be utilized by other industry owners to meet their own plastics recycling goals.
Brad Ives hopes to catalyze more such initiatives as the new director of the fledgling LSU Institute for Energy Innovation. Launched in June 2022 and funded by a $25 million gift from Shell, the institute serves as a national model for energy-related collaboration.
Ives says one of the institute’s primary goals will be to eliminate the hesitancy, and perhaps resistance, to the energy transition in both the public and private sectors, while also assisting industrial owners by identifying and implementing needed research.
“The transition will happen whether we want it to or not, so being prepared for it is the key,” he adds. “We’re making sure LSU is a trusted voice that can help bring the facts to the table.”
Outgoing interim director Rhoman Hardy, founder of Hardline Consulting in Baton Rouge, says the institute will introduce new technologies and innovative ways of doing business in Louisiana through a collaborative approach with industry. Half of the institute’s board of directors, in fact, is made up of industry owner representatives.
The institute is currently receiving study proposals “and we expect the first set of outputs from those studies early next year,” Hardy says. There are plans as well to modify LSU’s PERTT (Petroleum Engineering Research, Training and Testing) Lab to incorporate the study of hydrogen applications.
Louisiana Economic Development’s FastStart program is tackling another piece of the puzzle: giving workers the skill set they’ll need as the market transitions. FastStart provides recruitment, training and worker pipeline services when a company’s capital investment creates more than 15 net new jobs.
Paul Helton, executive director of the program, says the organization will soon offer training assistance for certain blue/green hydrogen and renewable energy projects. LED recently assisted Chalmette Refining, which last spring completed a new 306 million-gallon-per-year renewable diesel production unit at a cost of $600 million.
“Louisiana has been a petrochemical, oil and gas powerhouse for so long, but this doesn’t really change that,” Helton says. “It actually puts us in a good position. Our workforce has the skills that they need to go ahead and do this. They already know the processes.”
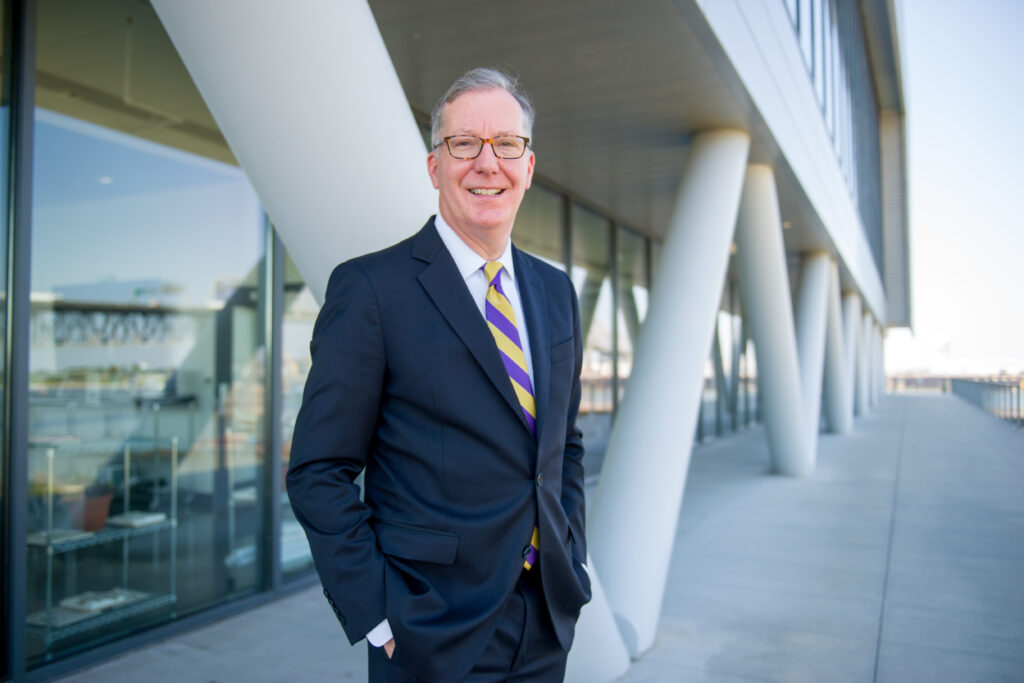
ROOM TO GROW
Eric Walker, Sasol vice president of operations, says half of Sasol’s 2,000 acres in Lake Charles are shovel ready, and that makes it an attractive location for sustainability partnerships.
In 2021, Sasol announced that it planned to reduce its greenhouse gas emissions to net-zero by 2050, with a shorter-term goal of a 30% reduction by 2030. Out of that vision came the Sustainability Hub, an effort to extract further value from the site and explore potential opportunities for co-location and growth. “It’s land that has been prepared for future growth opportunities,” Walker says. “It’s vacant and shovel ready for development.”.
Working collaboratively, Sasol Chemicals and Mission Possible Partnership are evaluating potential projects for the hub. In its role, MPP advises Sasol on a host of opportunities such as the use of hydrogen as an energy source, CCUS, and sustainable aviation fuel production, with the goal of advancing one or more projects to a final investment decision.
Sasol will provide subject matter experts to collaborate with MPP to determine the best paths forward. Most recently, MPP secured funding from the Bezos Earth Fund to support up to 10 industrial decarbonization projects, and identified Sasol’s Lake Charles facility as a location.
“We’re looking for strategic partners who have similar goals and who can build manufacturing complexes on our site through a partnership,” Walker says. “In turn, we’ll produce products that protect the environment and meet the growing demand for more efficient, sustainable products.”
Economic and COVID-induced slowdowns have given Sasol more time to be strategic in selecting potential partners. “We don’t think that’s necessarily a terrible thing,” he adds. “It gives us a little more time to evaluate different opportunities and to work on things that are going to be key for the partnership to be successful, such as workforce development.”
Walker hopes that the initiative will lead to multiple assets being located on Sasol’s Lake Charles property. “It might be joint venture opportunities where we form an entity that operates a facility together,” he says, “or we might have feedstock and property available that someone needs, where we provide feedstock or some other synergistic benefit.”
The Sustainability Hub offers unlimited potential, says Sarah Hughes, Sasol’s stakeholder relations manager. “We hope to utilize our expertise, as well as the expertise of other companies,” she notes. “Our peers have similar sustainability goals and ambitions, so why not tackle them together?”
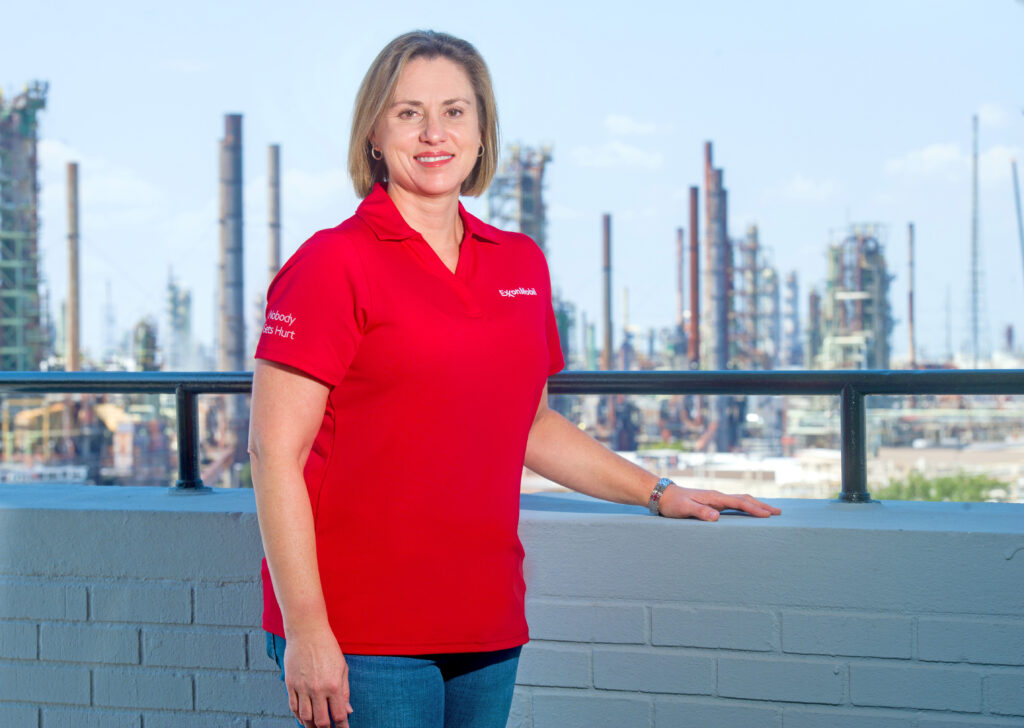
CIRCULAR POLYPROPYLENE
Jennifer Purpera, head of the Planning and Energy Department at ExxonMobil, says her team is campaigning hard to land a new advanced recycling plant in Baton Rouge. As the project development lead, it’s her job to bring those types of investments to the local plant.
“We’re trying to convince our management that the Baton Rouge facility is the right place for it,” Purpera says. “We present to our corporate headquarters director and management committee the value of certain investments and what they can bring for the company by using Baton Rouge.”
ExxonMobil plans to build advanced recycling facilities at many of its other manufacturing sites around the world, which would give it the capacity to process up to 1 billion pounds of plastic waste annually by the end of 2026. The company is considering building one such facility in Baton Rouge.
By breaking down plastics to the molecular level, the technology for advanced recycling creates the building blocks that can then be used to produce new virgin-quality plastic and other valuable products that can be put back into the value chain. It also results in lower greenhouse gas emissions when processing plastic waste than when processing the same amount of fossil-based feedstocks.
Having the advanced recycling plant built in Baton Rouge would be a huge win, Purpera says. Should the local facility land the project, it could potentially generate a significant amount of additional business from other companies looking for ways to recycle their own plastic waste.
It all fits into ExxonMobil’s goal of 1 billion pounds of recycled plastics by the end of 2026. In late 2022, an advanced recycling plant began operating on a limited scale in Baytown, Texas.
“The plant in Baytown was our beta test,” she says. “We’ve learned a lot as we developed the technology and used proprietary catalysts in this process. We’ve made some adjustments to the kit that’s required and to the types of plastic that we are capable of processing.” The plant has now ramped up to commercial scale, using a process that can be replicated around the world.
Purpera says that Baton Rouge holds a lot of potential as the next site.
“We’ve doubled the capacity of our polyolefins plant in Baker, which makes polypropylene,” she says. “If we were able to bring a recycling facility to the Baton Rouge area, that would allow us to amplify our ability to make circular polypropylene for some of our customers. That fills a need, as some of our customers are asking for plastics that are fully circular and made from 100 percent recycled content. Some of those plastics are difficult for mechanical recyclers to recycle.”
It all melds nicely with ExxonMobil’s 2050 net-zero emissions goals. Purpera says every operational site is tasked with proposing ideas for lowering emissions. “We’ve been working throughout the year to determine what technology and new equipment will be required,” she adds. “My team is in the early stages of that work now, in hopes of bringing those types of investments to the area.”