Technology is making great strides in enhancing the ability of maintenance workers to do their jobs more efficiently and safely, primarily through the manipulation of data. Industry 4.0, robotics, AI, virtual reality, machine learning and a host of other tools are all playing a role in transforming the landscape.
Kyle Daughtry, digital and extended realities solutions architect at ExxonMobil in Houston, says the industrial space is heading toward a more visual way of working. In February, he spoke at the annual Tec Next Conference in Baton Rouge. Nearly 200 attended the two-day event, during which industry and technology experts gave brief, 15-minute talks about various technologies.
“Industry data is moving at exponential speeds,” Daughtry says. “And it’s a tsunami of data—there has been a 4,300 percent increase in big data from 2016 to 2021. That’s significant, since it ultimately provides the foundational point for visual transformation.”
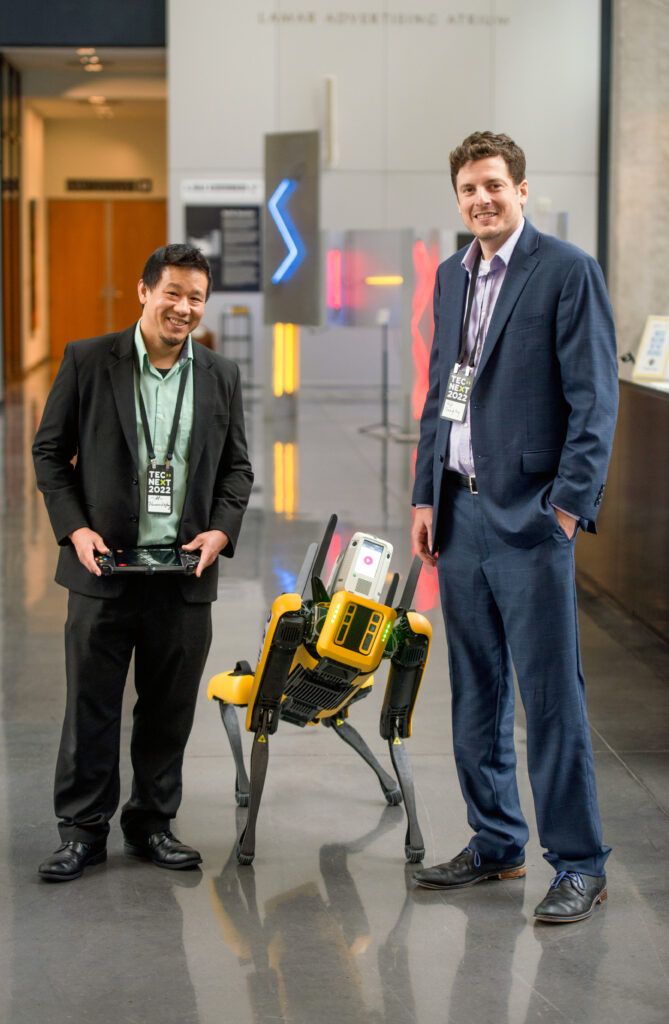
The “digital reality ecosystem” is becoming the new way of working at ExxonMobil. Data is being captured in real time and in a variety of ways, then accessed and manipulated whenever and however needed. ExxonMobil is finding that most of that data is best interpreted in a 3D, not 2D, world.
“We see a future where an operator has access to all of that information at their fingerprints, and in real time,” he adds. “It’s changing complete work processes in our industry, from being able to perform maintenance or engineering design in a collaborative environment, to putting yourself through high-consequence scenarios to emergency response.”
Working in today’s industrial space is a lot like playing a team sport, says Art Powers, ExxonMobil’s principal for Emergency Preparedness & Response in Irving, Texas. In both environments, there’s a common desire to accurately simulate “game time” conditions during practice. And like never before, Powers adds, immersive technologies are enabling industrial owners to do just that.
Powers was the opening keynote speaker at TEC Next. “Practice like we play is what we hear on our sports teams, but it boils down to simulating game-time conditions in order to perform at optimal levels,” Powers says. “That’s part of what we do every day in the industrial space. It just has a different terminology associated with it … walk throughs, dry runs, beta testing, etcetera.”
As for its part, ExxonMobil created an Immersive Technologies Studio at its Houston campus in 2019 and manned it with experts in the fields of learning, collaboration and design. Along the way, they’ve identified existing technologies and synced them with the needs of the company.
“We’re all technologists at heart, and we are taking on real challenges in our work,” he adds. “Our Immersive Technologies Studio tries to create that synergy.”
INDUSTRY 4.0 IS VITAL
Rishi Vaish, chief technology officer and vice president of AI applications at IBM, says Industry 4.0 will be critical to the future of maintenance.
“The things people are wanting to accomplish in the industrial space … reduce operational costs, gain efficiencies, extend the lifetime of their assets, those questions haven’t changed throughout all of the various industrial revolutions,” says Vaish in addressing the Tec Next audience. “It’s just the kind of tools that you have to solve those problems that have changed, and quite dramatically.”
Blockchain solutions, AI-based applications, hybrid cloud technologies, cloud computing, software-as-a-service architecture and application middleware as all necessary parts of the 4.0 matrix.
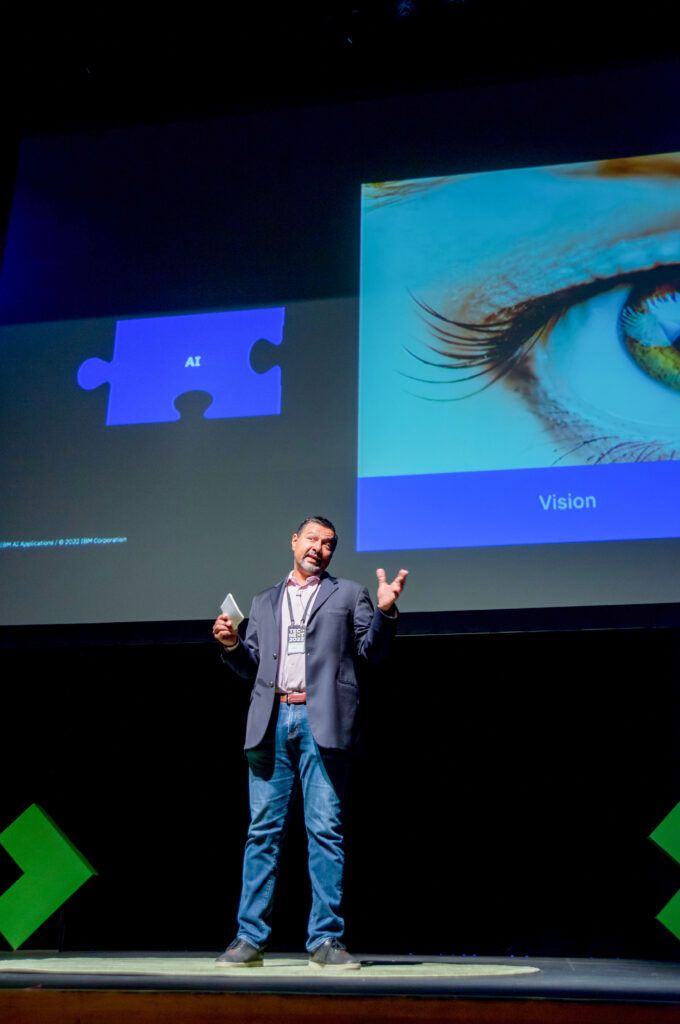
Much of them are easily transferrable to the maintenance space. “We all have a ‘digital twin’ online, and you can do exactly the same thing for every asset in your plant,” Vaish says. “You have data on these assets, such as the manufacturer, the date you installed it, the various performance measurements that you take … that makes up that digital profile.
“You can then take that data stream and put it somewhere in a digitized database, then mine that data however you like,” he adds. “Typically, you want to get this data from sensors installed by the manufacturer, or from sensors you add around your devices—cameras, temperature gauges etcetera.
“This is a way you can transform your operations without having to make a lot of physical changes to what you do,” he adds. “The data from your digital twin is what AI needs.”
Vaish is most excited about AI’s future potential. He says current AI applications in the auto manufacturing industry can be easily transferred to industrial maintenance. “We helped one auto manufacturer create and load an application onto their phone, which can then be pointed at an assembly and immediately tell them if there’s a defect. It has revolutionized the speed of their assembly line and the number of defects that they find.”
It can also considerably reduce safety risk. “You can deploy these same visual inspection and recognition technologies via a robot that can go into areas that are unsafe without putting workers at risk,” he adds. The same technology can also be deployed on drones.
NOTHING WORKS WITHOUT CONNECTIVITY
Kit Keen, a senior technology consultant at engineering firm MS Benbow & Associates in Metairie, says regardless of the technology, it’s only as effective as the internet connectivity available within the plant. “We’re trying to integrate a lot of things … and without wireless connectivity where are we? It’s that non-sexy but necessary conversation when you’re thinking about implementing the next technology.”
The cellular industry has done a good job of providing Wi-Fi coverage in the public domain, but the industrial environment has been traditionally overlooked, Keen says, largely due to security concerns and a reluctance by owners.
Private LTE (Long-Term Evolution) is the answer, he adds, as it provides a way to alleviate those concerns.
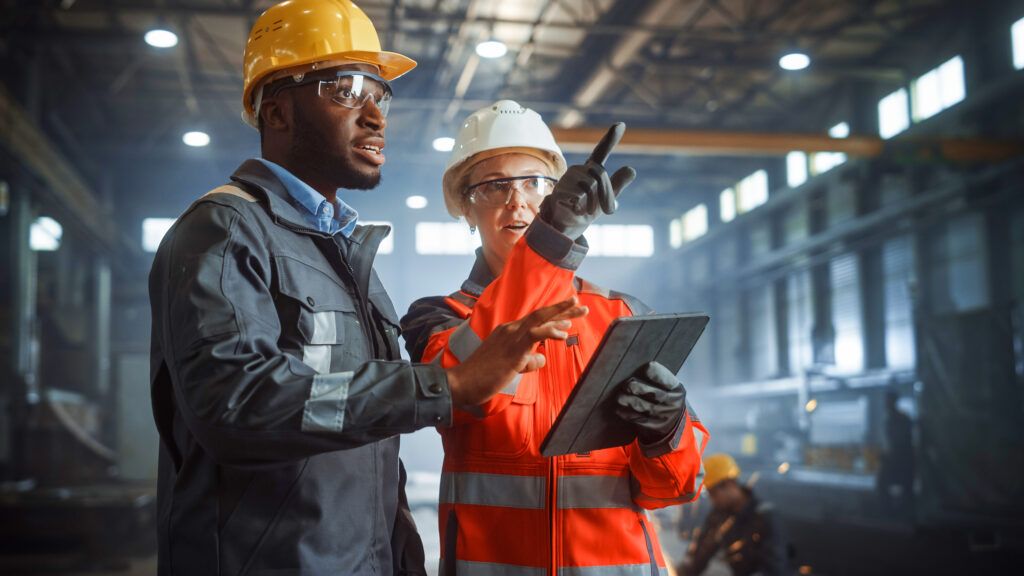
LTEs enable mobile data to be transferred in larger amounts and at higher speeds than was possible under earlier wireless communication standards, while Private LTE offers network scalability, increased security, SIM-based authentication and administrative control. “If you’re in an outdoor environment, Wi-Fi doesn’t do a good job for people and assets moving in a 3D space,” Keen says.
“Private LTE has matured significantly over the last couple of years and allows for owners to build and own their own private LTE system with the features of a public system.”
Seamless mobility is perhaps the biggest advantage it offers the maintenance space. “There is the benefit of seamless handoffs throughout the coverage area,” he adds.
“And it comes with network speeds and bandwidths comparable to Wi-Fi, with increased reliability, and an increased indoor and outdoor coverage footprint.”