It didn’t take long for the record-breaking August deluge of 30-plus inches of rain in and around Baton Rouge—and the flooding that followed—to escalate into a tragedy of epic proportions, leaving thousands homeless and in need of immediate assistance.
While the area’s industrial facilities were mostly spared from the rising waters, thousands of workers from a five-parish area weren’t so fortunate. On average, the flood directly impacted an estimated 20% of permanent, full-time employees of area plants.
“Unlike Katrina, our plant operations were not severely affected,” says Dan Borne, president of the Louisiana Chemical Association. “With perhaps one minor exception, power was not interrupted, as it was in Katrina. Natural gas supplies were not shut off, as they were in Katrina, and business supply chains (rail, barge and truck transportation) were not severely delayed as they were in Katrina.”
However, Borne estimates that about two-thirds of the state’s chemical manufacturing employees live or work in the parishes affected by the flooding. “While we don’t have plant facilities in Livingston Parish, which was really hit hard, it’s a bedroom community for many or our employees and for lots of members of LCA.”
The major challenge for plant owners in the flood’s immediate aftermath was assisting employees and helping them return to work—because the plants continued to run—and to help them rebuild their homes and restore their lives.
Bob Johnston, ExxonMobil Chemical site manager, says adequately planning for this disaster was impossible. The company’s Baton Rouge area plants had an astounding 500 employees directly impacted by the flood. “It was unlike anything we’ve been through,” Johnston says. “The lack of advance warning and the scope of the impact was unprecedented.”
While many employees were already involved in various stages of search-and-rescue as members of the Cajun Navy, one of ExxonMobil’s first official actions was to contract a company called Red Hawk of Baton Rouge to mobilize up to 65 three- to five-person crews to tear out sheet rock, clean out debris and remove furniture and cabinets from employee homes.
Additionally, some 300 ExxonMobil employees mobilized as volunteers. “As people worried about getting their homes clean and tried to figure out how they were going to continue to work,” Johnston says, “it was really about providing someone to get in there and help with that critical first step.”
‘Can you help us?’
Vanessa Bailey, an eight-year employee at ExxonMobil and a resident of Denham Springs, found herself at “ground zero” the morning of Aug. 13. “We left the house headed to soccer, then got a call that it had been cancelled,” Bailey says. “By the time we got back, the back part of our neighborhood was already flooding.” Before long, the entire neighborhood was under water, as was her car.
That was when she noticed someone with a truck and an ExxonMobil hang tag on the rearview mirror. “I was like, ‘I work at Exxon. I see you work at Exxon. Can you help us?’ So we jumped in the truck with him. I didn’t even know who the guy was.” Brandon White, an ExxonMobil chemical plant process operator, was Vanessa’s savior that day, and had been in the neighborhood checking on one of her neighbors.
Brandon’s goodwill didn’t end there. Since his house had not flooded, he let Vanessa and her son stay there for four days. All the while, he kept them in food and clothing until Vanessa could return home. “During all of this, I was keeping up with my bosses,” she adds. “I let them know when we were going to try to get back to the house, and by the time I got there about four of my co-workers were pulling up behind me.”
In the days that followed, co-workers brought a generator and a saw to cut sheetrock, and Red Hawk assisted with debris removal. “I was literally in tears when these guys showed up with shovels, an ice chest and food to come help,” Bailey says. After three days, “all that I had left were studs and a toilet.” Ultimately, Vanessa missed seven days of work.
Helping employees in need
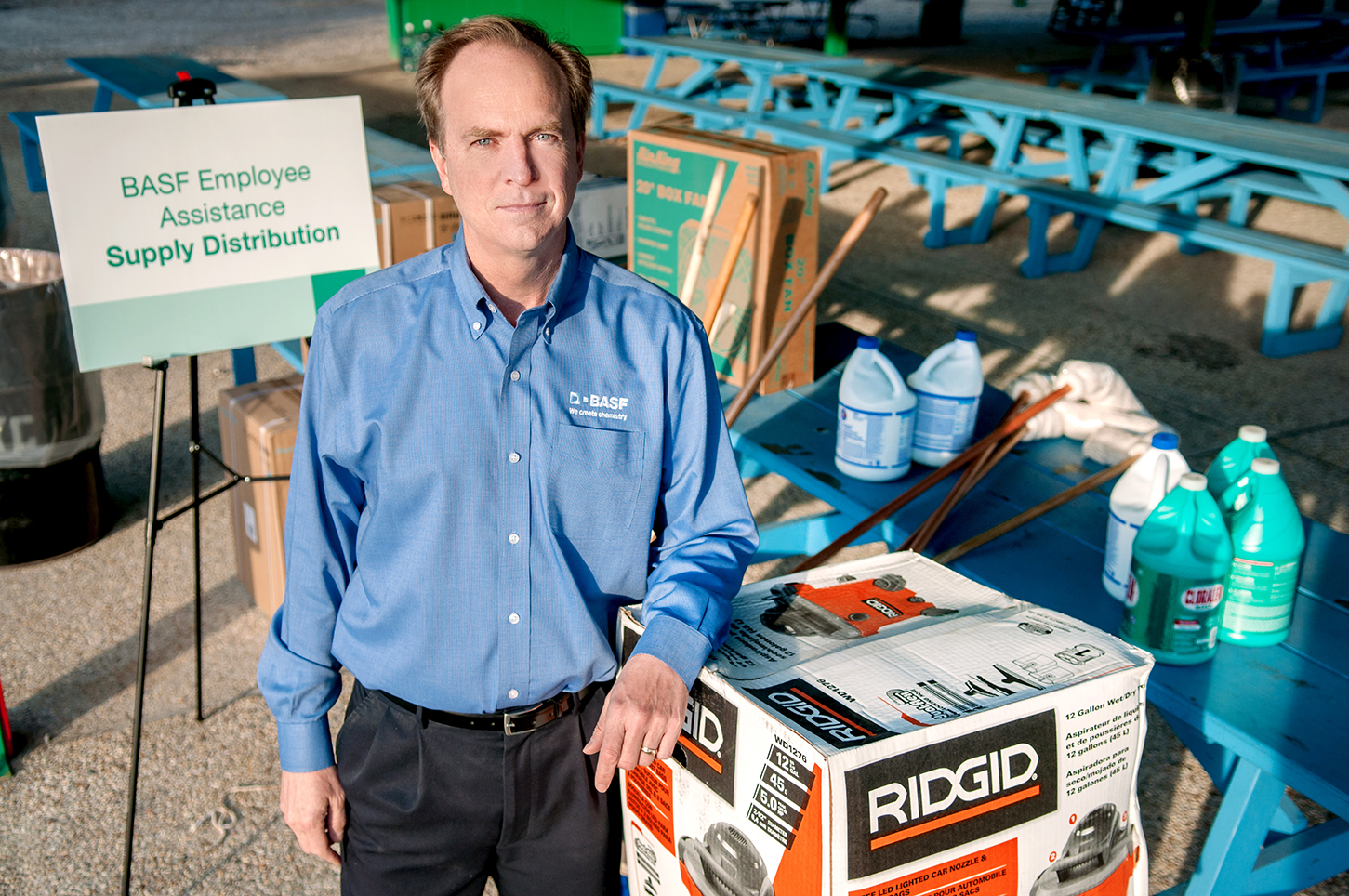
Vanessa’s story is similar to many across the parishes affected by the flood, as plants stepped up to help employees in their times of need, whether materially, financially or through hands-on cleanup.
BASF in Geismar quickly mobilized a task force to determine needs, and locate and acquire necessary housing, transportation and supplies for its impacted employees. “We actually did not have a specific plan for an event like this,” says Tom Yura, senior vice president and general manager of BASF in Geismar. “You pull out everything you know. You pull out your hurricane plans and your incident command plans. You pull out your cooperative efforts within the broader community and you start working on it.
“When a crisis like this occurs, you don’t typically have days to sit back and contemplate next steps. You’ve got to move fast. You have to move decisively and you have to think about people above everything else.”
In addition to BASF’s impacted employee population of 300, another 30% to 40% were either surrounded by water or had family members who were homeless.
BASF’s leadership team designated three people to lead the recovery effort: one to coordinate communications; one to determine needs for lodging, food, clothing and transportation; and a third to procure those needs. “We became a forward staging area for employees, where we brought in supplies for remediation and for immediate needs such as food, clothing … or even toys and baby supplies.”
Many plants in the area were similarly affected, although at different scales. At Dow’s Louisiana Operations in Plaquemine, the flood stranded more than 160 of its 1,400 employees, but the impact to its contract work force was particularly significant.
“We were gearing up for a large turnaround, and it was a challenge to get that contract workforce back to work,” says Public Affairs Director Stacey Chiasson. “We were about 70 percent after the flood, as far as the contract workforce coming back, and that slowly picked up.”
Within days, the Dow Chemical Co. Foundation had donated $250,000 to support the recovery efforts, and an additional $50,000 apiece to the Capital Area Chapter of the American Red Cross and the Capital Area United Way Flood Emergency Fund.
Dow also offered interest free loans to those employees in immediate financial need. “We went to a three-pronged approach,” Chiasson says. “How do we help with dollars from our foundation? What do we do from an employee engagement standpoint? And what’s our influence and partnerships and relation with businesses and customers?”
At Shell Chemical in Geismar, about 100 employees (of 650) were impacted, prompting the plant to organize “special benefits for those people who were impacted,” says plant manager Rhoman Hardy. “That includes salary continuity, low- to no-interest loans, etc. We also organized crews to help them gut their homes.”
Plants also turned to customers for help in the flood’s wake.
Dow approached Proctor & Gamble for assistance through Tide’s Loads of Hope program, which was created following Hurricane Katrina. Loads of Hope is essentially a mobile Laundromat developed to restore a sense of normalcy for victims of a disaster.
“We worked with them on where to go, what the needs were, etc.” Dow’s Chiasson says. “They set up at a local church, and we were able to get word out to our employees.”
BASF customers also stepped up to help. Future Foam delivered 200 queen-sized beds and more than 500 mattress toppers to BASF’s administrative offices, where employees could pick them up. “We actually produce the chemistry for those products,” BASF’s Yura says. “When you mix the materials together you get the foam that goes into the mattresses.”
LCA’s Borne points out that most of the products used during the cleanup contained chemical products made in Louisiana. “Succinctly put, if you can name it Louisiana chemical manufacturing helped make it,” he adds.
A new disaster game plan takes shape
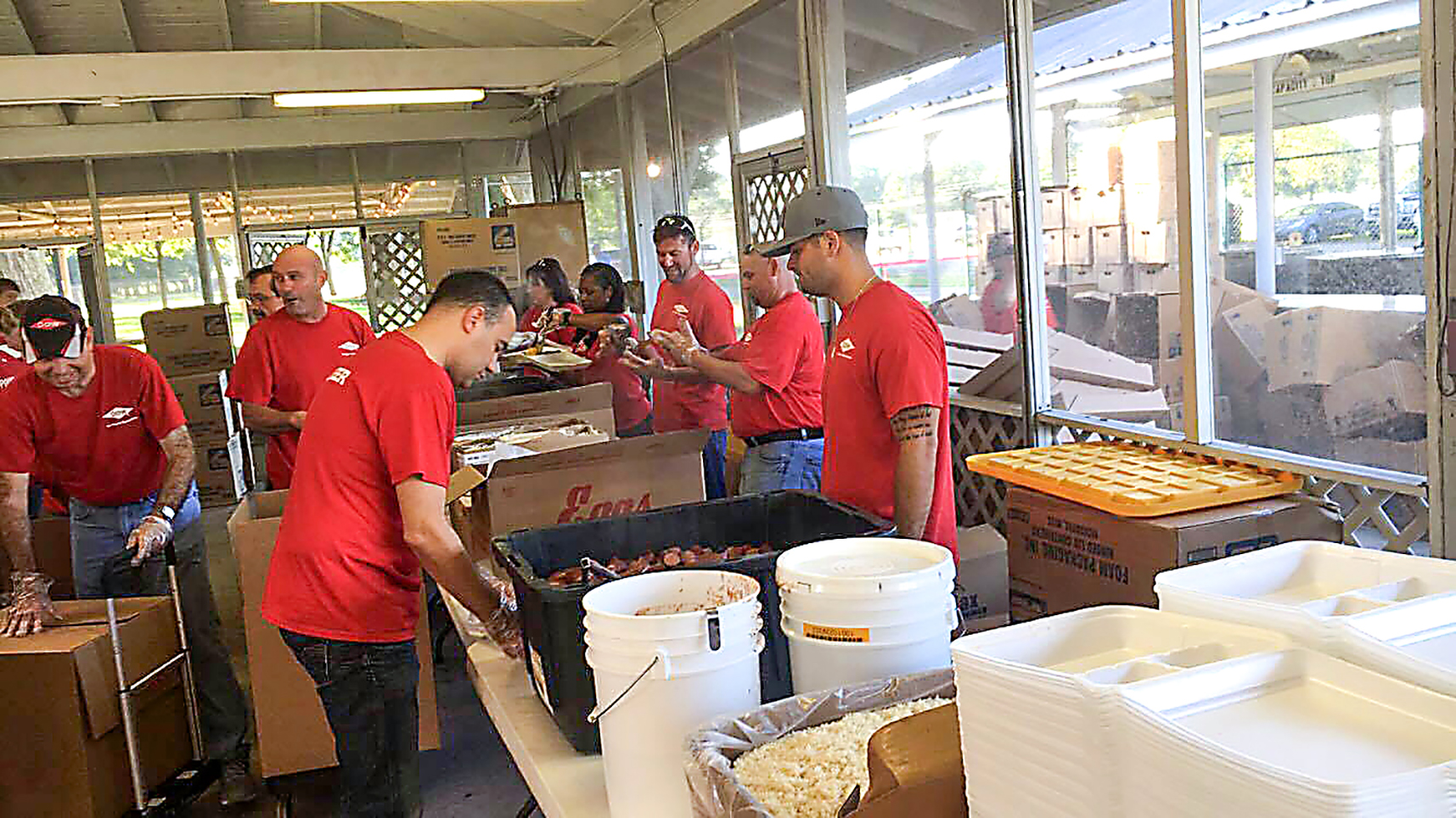
At BASF, it didn’t take long before the “lessons learned” from the flood of 2016 were put into practice: Hurricane Matthew hit the company’s Savannah, Georgia, site just a few weeks later. “Our team reached out to that site and we ran down our list of ‘Hey, think about this, or we used this technology. Or, here are the types of supplies you might want to consider,’” Yura says.
As with any disaster, many plants performed a plus/delta evaluation following the storm to determine lessons learned and implement best practices going forward. One such “best practice” for BASF was utilizing neighboring plant sites as a forward staging area for stockpiling necessary supplies and equipment.
“We’re quick learners and we’re doing a lot of documentation of this event,” Yura adds. “When you’re moving fast, sometimes you just shoot out numbers and then you may overshoot or undershoot; so we refine that and document it and put it into our emergency plans moving forward. Most importantly, we share it within the corporation.”
ExxonMobil’s Johnston says many of the lessons learned from the flood revolve around the effective use of communications.
“I don’t think any of us really expected the scope of the communications challenges,” Johnston says. “One of the biggest problems was connecting with folks who no longer had a home phone, or even an operating cell phone.”
As one remedy, ExxonMobil set up an external website with resources for employees that could be accessed by cell phone or any computer.
Dow’s Chiasson says what worked during Hurricane Katrina didn’t necessarily work during the flood of 2016. As such, Dow’s plus/delta process will examine the effectiveness of established procedures in order to identify policies and processes that need changing or revising.
Dow also found communications to be one of the most significant initial challenges. “While we work a phone tree system during disasters, we’ve learned that social media is particularly useful in such situations,” she adds. “When the phone lines are out, sometimes they can still go to Facebook and see how to contact their supervisor. That’s how we were able to push out a lot of messages and get information back from our employees.”
She adds that other issues will be addressed in the coming months. “I think we’re looking at going about things differently when addressing mental health issues and homelessness that result from these events. It’s eight weeks later and people are nowhere near going back to their homes. What’s the long-term effect of that? That’s important to us.”
The financial burden
Begun in the aftermath of Hurricane Katrina, the Baton Rouge Area Foundation’s Employees 1st program partners with companies provides cash grants to their employees facing unexpected difficulties. Employees are also encouraged to make tax-deductible donations to the fund.
The program expanded from just 10 employee assistance funds to 80 in the aftermath of the storm, as area businesses leaned upon the program to disseminate financial assistance to their employees.
In the wake of the flood, numerous plants and industrial contractors have established Employees 1st accounts, some of which include Dow, Formosa Plastics, Georgia-Pacific, MexiChem, Pala Industrial Construction, Praxair and Associated Builders and Contractors Pelican Chapter. To get started, these companies made a minimum seed deposit of $10,000, then employees were encouraged to make a tax-deductible donation to build the coffers.
“Certainly, depending upon the employee base, sometimes you want to have more than that, but in general that’s the starting point,” says Elizabeth Hutchison, Employees 1st project manager at BRAF. “We have research data that helps us determine what we recommend keeping in the fund, and how many of their employees might face one of these qualifying incidents in a calendar year. We really work with each company based upon their needs, their employee base, and customize their fund according to their need.”
The funds are controlled entirely by BRAF within an investment portfolio managed by Goldman Sachs and J. P. Morgan.
Hutchison says the process works fairly quickly after an employee submits an on-line claim. “Within 48 hours they have an answer of ‘Yes, your incident qualifies,’ or it’s denied for whatever reason,” she adds. “Then within a week tops, if not sooner, you receive a check if approved.”
Originally published in the fourth quarter 2016 edition of 10/12 Industry Report.