A number of unplanned events can impact a plant’s reliability and resiliency in south Louisiana. Material delays, inflationary pressures, hurricanes, high river levels, unprecedented winter weather and manpower shortages all bring their own unique challenges.
But what happens when they all occur over the course of a year or two? Plant leaders say that perfectly describes 2020-21, as no amount of resiliency planning could have prepared them for the chaos caused by the COVID-19 pandemic, unprecedented supply chain disruptions, a freak ice storm and the largest hurricanes to make landfall in the state’s history.
Even prior to the pandemic, though, academia had begun to tackle the problems of reliability and resiliency along the Gulf Coast.
With Texas A&M acting as lead, LSU, Mississippi State University, Tuskegee University, the University of Texas at Austin and Florida Atlantic University embarked on an effort in 2019 to anticipate, mitigate and respond to the impacts of natural disasters on the reliability of manufacturing value chains.
The group is currently developing a holistic, innovative, convergent, and scientifically driven platform that enables the creation of resilient technologies, decision-making frameworks, methodologies and tools. The research is being funded by a National Science Foundation Engineering Research Grant.
To provide a venue for sharing their own best practices, 10/12 Industry Report sat down with four area industry leaders to discuss their methods for ensuring reliability during unplanned events, as well as some of the lessons learned over the last 24 months.
MEET THE PANEL
Jeff Blohm, site mechanical manager, ExxonMobil Baton Rouge
Shanna Noble, Turnaround and Construction Department Head, ExxonMobil Baton Rouge
Kristie Pickering, director, utilities and infrastructure, BASF Geismar
Brent Robinson, director, maintenance, reliability, machinery & integrity expertise, BASF Geismar
WHAT HAVE BEEN THE PRIMARY OBSTACLES TO DE-RISKING YOUR PLANT FROM RELIABILITY PROBLEMS OVER THE LAST TWO YEARS?
Kristie Pickering, BASF: Not all suppliers have the same commitment and mindset related to reliability, so overall reliability can be impacted. A rigorous approach is required to improve reliability and minimize the impact from unplanned events. Another obstacle can be logistics. This is difficult to overcome in a storm event, but we work closely with providers to ensure we can get product to customers as soon as it’s safe to do so. Finally, when an unplanned event occurs, it often impacts our employees. BASF does an excellent job of supporting employees and the community during these events. During Hurricane Ida, employees were offered fuel, housing support and supplies to make temporary repairs to their homes.
Brent Robinson, BASF: The supply chain situation is continuously changing due to the pandemic and other global impacts. Components and services that were readily available in the past may not be available today; this presents a significant challenge to de-risking our assets. Identifying, training and retaining human talent is another important factor to de-risking our facilities during unplanned events. BASF has partnered with local resources and focused internally on strong mentoring and training programs to strengthen the talent pipeline required to plan for and react to non-typical events.
Shanna Noble, ExxonMobil: We continue to invest in maintaining logistics flexibility across ExxonMobil facilities, since unplanned events can impact crude and other feedstock availability as well as product outlets. Support from governments, our commercial partners and other suppliers, such as Entergy, is critical. During Hurricane Ida, the Baton Rouge Refinery utilized the Strategic Petroleum Reserve to maintain crude supply and to continue to supply the local market with fuel.
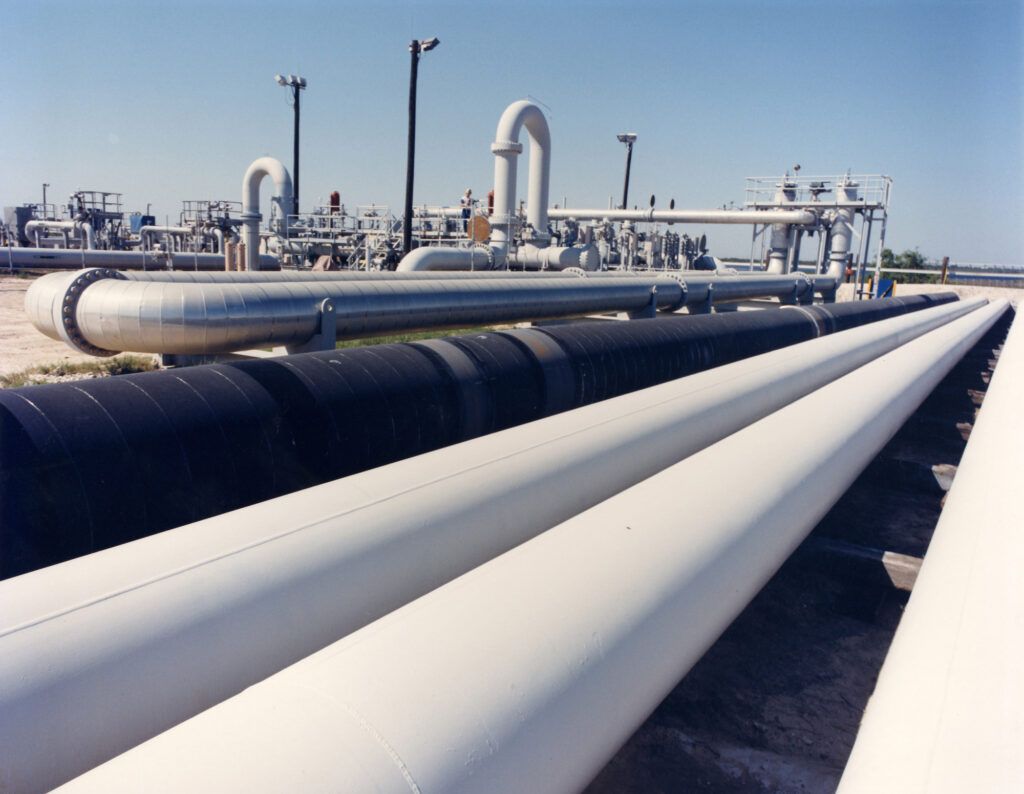
DURING AND AFTER AN EVENT, WHAT IS YOUR PROCESS FOR CAPTURING AND DISSEMINATING LESSONS LEARNED?
Jeff Blohm, ExxonMobil: For external events where we have time to prepare, such as hurricanes, we have internal emergency preparedness plans and procedures to prepare for the event and minimize customer impacts. This includes collaboration and planning across the Baton Rouge area ExxonMobil facilities and with contract partners to maintain production to the extent possible without compromising the safety of our employees, contractors and community.
For Hurricane Ida, we were able to provide fuel supply to the region from our Baton Rouge Fuels Terminal due to planning and coordination within our company and via collaboration with distributors, contractor firms, suppliers and other industry members.
For unexpected events, we have backup systems in place, such as redundant power and logistics flexibility (such as various feedstock sources and product outlets) to help minimize production impact. For each of these events, we capture lessons learned internally to enhance our response plans in the future.
Kristie Pickering: For unexpected impacts to production, BASF takes the opportunity to learn from these events. We investigate what happened and take actions to prevent a recurrence. Some items are straightforward and can be solved with a few people. The more complex ones require a formal Root Cause Failure Analysis, or RCFA.
Others may require multiple teams or RCFAs, such as an impact from a hurricane or freeze. Action items are tracked in a database to ensure timely completion. BASF tracks asset effectiveness data on a global basis, and this gives us visibility into the effectiveness of our reliability programs in driving down unplanned losses. One lesson that is key from these events is preparedness. Over the years, we’ve continued to enhance our preparation checklists for events as we have new learnings.
Brent Robinson: In addition to Kristie’s comments, BASF has learned it is critical to anticipate failures in advance and develop mitigation plans to eliminate or reduce the impact of the event. This requires a commitment and dedication to complete a thorough review and implement actions as appropriate. This frontend work ensures proper plans, spare parts and supplier networks are established well in advance of an unexpected production interruption.
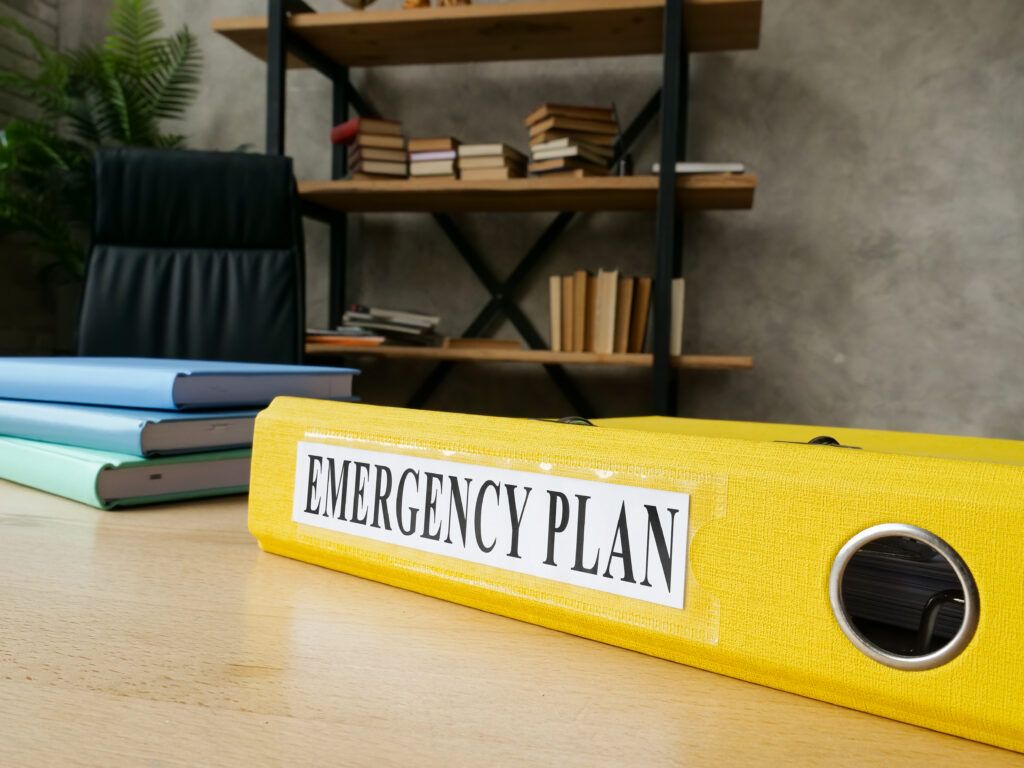
CAN WE EVER REACH A POINT WHERE RELIABILITY IS UNAFFECTED BY UNPLANNED EVENTS? WHY OR WHY NOT?
Jeff Blohm: At ExxonMobil, we are able to use our global, integrated footprint to help maintain supply reliability. For example, in the event of a hurricane in the Baton Rouge area, we would look to leverage company logistics and integration to supply local customers with products out of Texas or other ExxonMobil facilities.
Kristie Pickering: I’ve seen great improvements in our ability to ride through unplanned events. For both the 2021 freeze event and Hurricane Ida, BASF’s site in Geismar was able to maintain essential utility production—a much-improved outcome compared to impacts from Hurricane Gustav in 2008 and the 2018 freeze. Significant companywide efforts and spending were required to harden key systems to allow for continued utility production. For safety precautions, BASF shut down the production units during Hurricane Ida, but maintained key utilities to allow for less impact and more efficient startups after the storm passed.
During the pandemic, the risk we experienced was maintaining adequate staffing. Our plan called for systemic tracking of staffing and availability, trigger points for escalation and a backup staffing plan. This tracking allowed us to maintain the necessary staffing for critical operations. We knew our reliability was essential to our customers, especially those customers who we helped create life-saving products during the pandemic.
Brent Robinson: BASF continuously strives and works towards the ultimate goal of zero unplanned events impacting production so we can deliver on our promises to customers. BASF’s ability to eliminate impacts depends largely on two main factors: our ability to predict unplanned events and develop proper plans for prevention, and the associated business case for implementing the solutions.
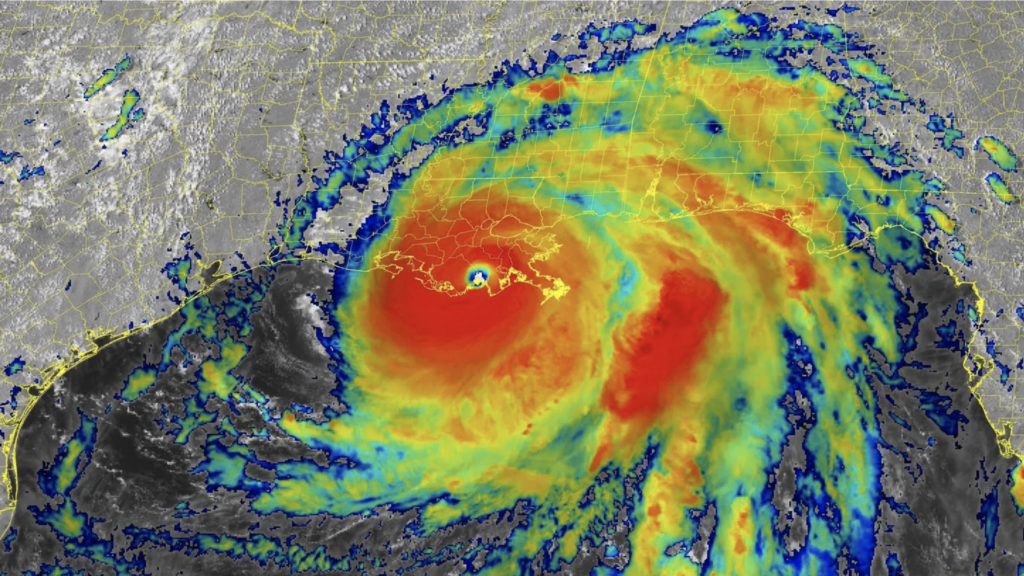
DOES INDUSTRY COLLABORATE TO ADDRESS RELIABILITY CONCERNS AND IN PLANNING FOR DISRUPTIVE EVENTS? IF SO, HOW?
Shanna Noble: Yes, we collaborate and plan with local and state organizations—the Mayor’s Office of Homeland Security & Emergency Preparedness, Governor’s Office of Homeland Security and Emergency Preparedness, Baton Rouge Area Mutual Aid System and the North Baton Rouge Chemical Industry Task Force—to ensure we are aligned on emergency preparedness plans across the region, share expertise to support mutual aid responses and ensure strong communication systems. We also work with our contractor firms and their areas of expertise to help our sites manage through situations.
Additionally, we maintain strong working relationships with feedstock and energy providers, such as Entergy, to ensure plans are in place for unplanned events. LSU is an educational partner with the fire training facility, where our volunteer fire team can train and support mutual aid learning. Finally, trade associations such as the Louisiana Mid-Continent Oil & Gas Association, Louisiana Chemical Association, and the Greater Baton Rouge Industry Alliance bring opportunities to share best practices in emergency preparedness.
Kristie Pickering: From an industry perspective, we are very connected. We often share suppliers and have supplier/customer relationships, so plant operations are integrated across companies. We also share key lessons learned and best practices through industry organizations, such as LCA and GBRIA.
Brent Robinson: In addition to the connection with suppliers and peers and industry organizations, we are also active participants and contributors in many technical organizations that are focused on improving supply reliability, such as the American Society of Mechanical Engineers, Institute of Electrical and Electronics Engineers, Society of Maintenance and Reliability Professionals and others.