The general public does not typically associate the petrochemical industry with environmental mindfulness. On the contrary, much of the descriptive language these days portrays industry as having a reckless disregard for its ecological setting.
To dispel these misconceptions, some owners have made it their mission to exceed required environmental regulations to ensure a healthy ecosystem. There is a growing, widespread recognition that industry and nature must co-exist to achieve a sustainable future.
The Louisiana Department of Environmental Quality is playing a key role in encouraging such endeavors, chiefly through its Environmental Leadership Program. The program promotes voluntary pollution prevention, waste reduction and other environmental stewardship efforts, then recognizes champions of the environment during an annual awards program.
Here’s a look at some of the previous ELP winners, and others who have gone above and beyond to protect the natural environment.
Flare Gas Minimization & Propane Treater Catalyst Upgrade
Alon Refining, Krotz Springs
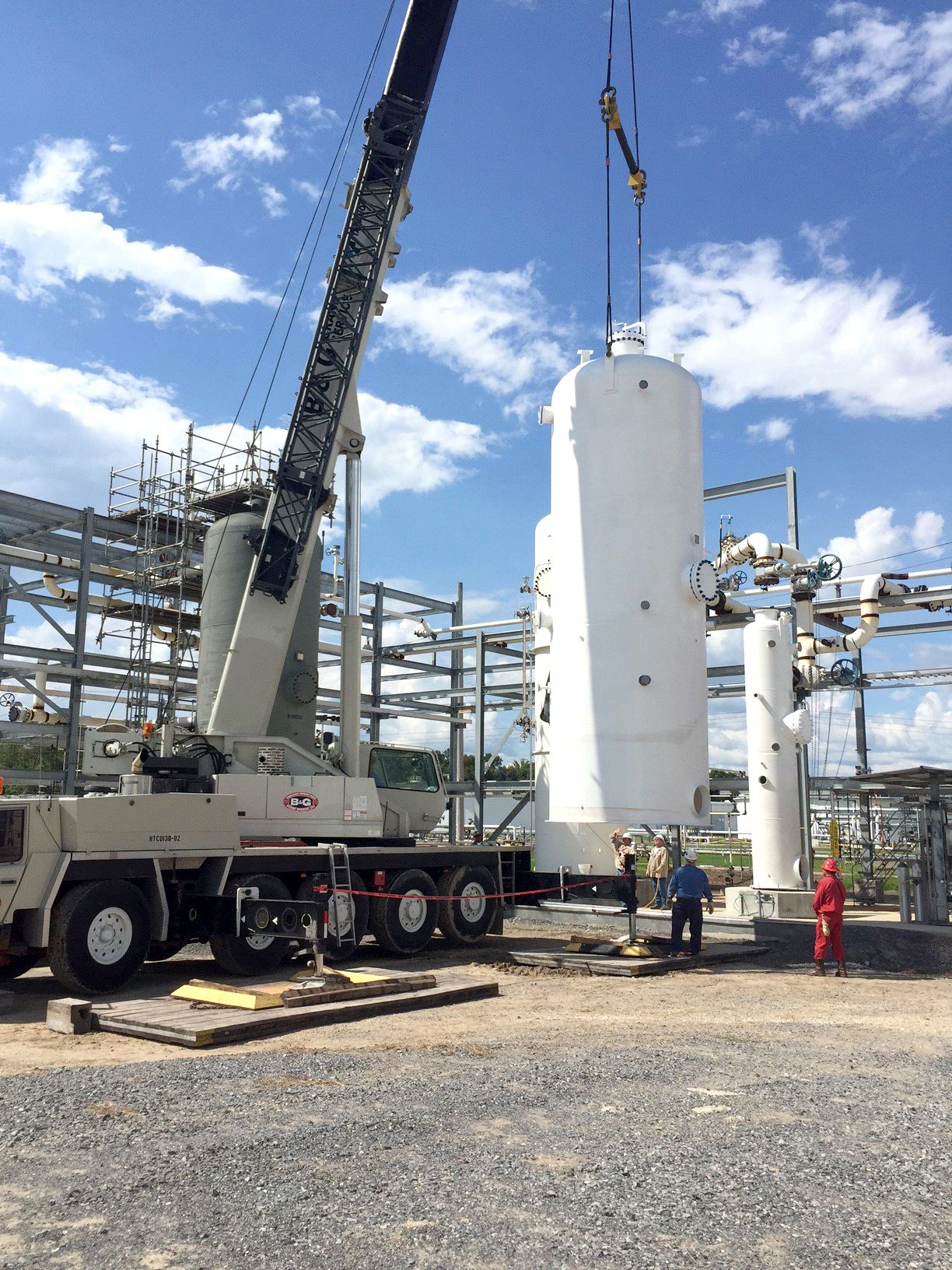
In a voluntary move, Alon Refining in Krotz Springs identified the product streams routed to its two flares—Crude Complex and the FCCU Complex—then removed or minimized the streams and installed sulfur removal systems on each flare. Flow measurement systems illustrate a reduction in flared gas of approximately 46 MMscf per year, allowing more gas to be recovered as product instead of being destroyed by the flares.
The result is a reduction in emissions of approximately 30 tons per year. In addition, the sulfur removal systems reduced hydrogen sulfide concentrations in the crude flare gas by more than 95% and in the FCCU flare gas by more than 99%, leading to a reduction in sulfur dioxide and hydrogen sulfide emissions of approximately 12 tons per year.
Additionally, during upgrades to its Propane (C3) Treater Catalyst, the refinery implemented a new layered absorbent-type catalyst in place of potassium hydroxide as a catalyst to remove sulfur compounds from propane products.
The new catalyst is longer lasting and non-hazardous, which simplifies the removal and replacement process and results in a 90% reduction in spent catalyst from the treatment process, or about 485 tons per year.
Bayou Verdine, Phillips 66, Westlake
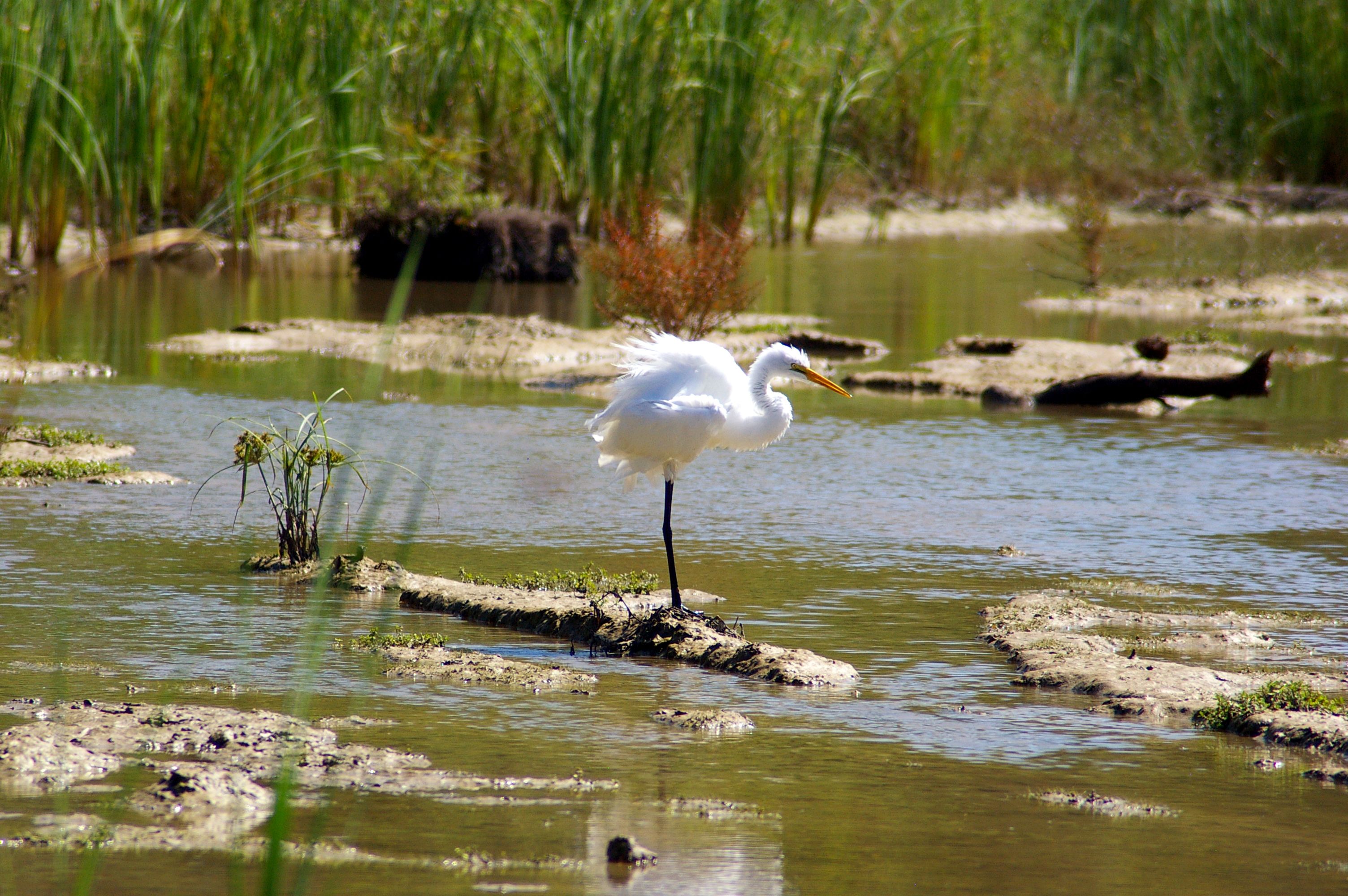
Phillips 66 in Westlake spearheaded an ecological revitalization project on Bayou Verdine, a shallow, tidal channel that runs through its property. The bayou flows into the Calcasieu Estuary, an important nursery for fish and wildlife. To remove historical industrial contamination, about 1.5 miles of the bayou was dredged and the contaminated sediments were placed in a containment cell that was capped upon completion.
The construction was topped with native grasses and wildflowers, which require little to no maintenance and will re-seed on their own.
BIOX Basins Facility, ExxonMobil Refinery, Baton Rouge
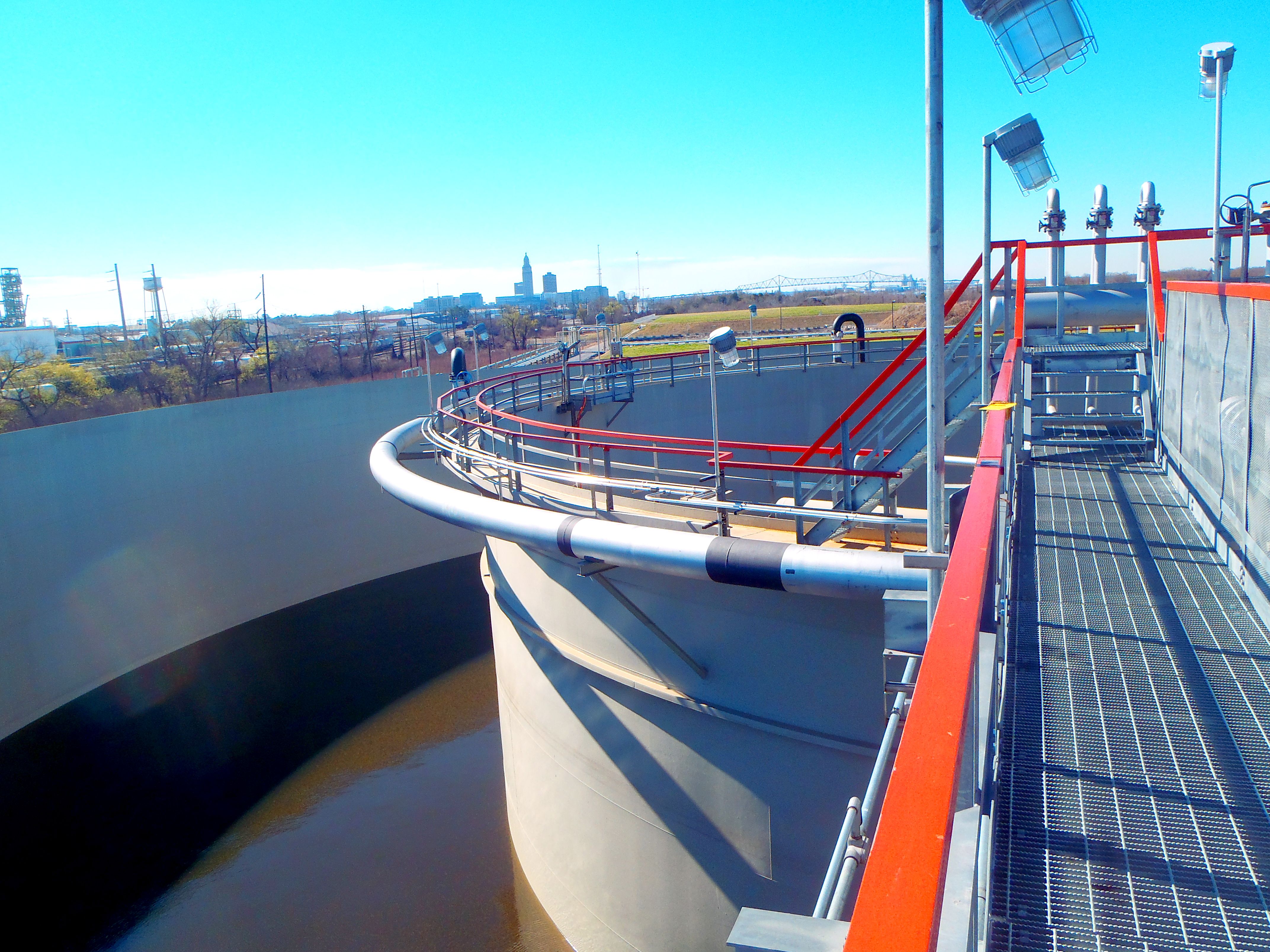
The ExxonMobil Baton Rouge Refinery’s two biological oxidation (BIOX) basins help reduce nitrate emissions in wastewater discharged into the Mississippi River well below required levels. The project included the construction of a new above-ground system for cleaning wastewater to replace the previous treatment basins. An additional investment proactively reduces wastewater discharges also well below required levels.
Historically, the Baton Rouge Refinery has contributed less than 1% of the nitrates in the Mississippi River. This project helps to reduce that amount by about 50%. The system has also helped reduce the refinery’s overall reportable releases to the environment, including air emissions, water discharges and offsite waste transfers, by 30%.
Hydrochloric Acid Handling & Aerogel Insulation, Rubicon LLC, Geismar
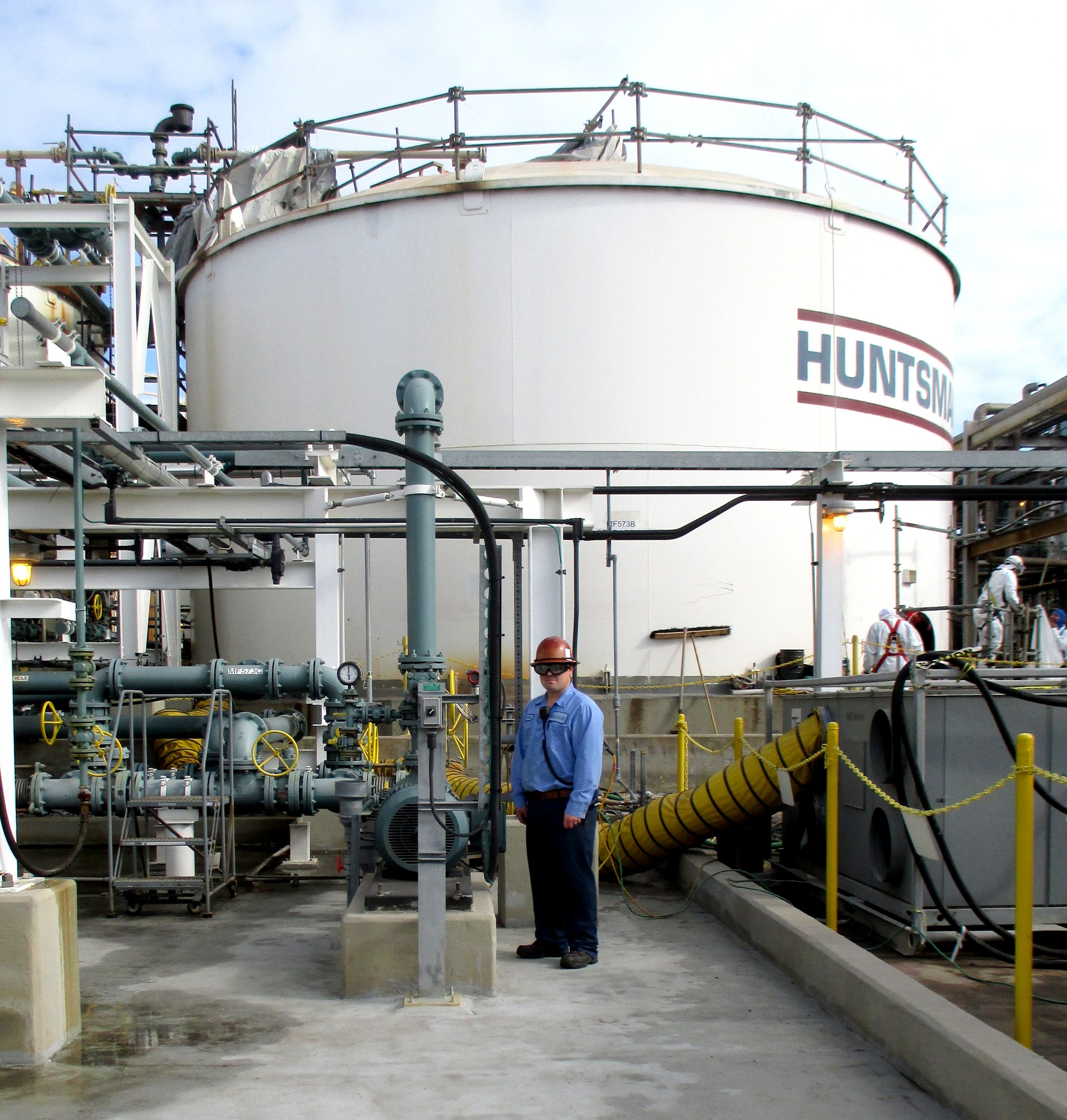
Rubicon’s Variants Plant in Geismar implemented hydrochloric acid handling improvements that included a new transfer pipeline routed directly to the customer. With the pipeline in place, Rubicon used 4,266 fewer tank trucks and rail cars to send HCl to customers in 2016. The pipeline has also reduced wastewater generation by approximately 21,000 gallons.
In another environmental move, Rubicon’s Risk-based Mechanical Integrity and Maintenance teams began using energy-efficient aerogel insulation due to its water repellant properties, thereby eliminating the risk of CUI (corrosion under insulation).
Also, the plant was awarded the International Green Apple Award for Environmental Best Practice for its Aniline Complex Benzene Recovery Project, which eliminates the incineration of an average of 722,000 pounds of benzene from the waste stream annually. In 2017, the site recovered and recycled 1.2 million pounds of benzene.