A pair of LSU professors hopes that their current research could one day turn robotic exoskeletons into reality in the construction space. In the process, they’ll improve worker safety and efficiency, and perhaps even create more opportunities for older workers and women.
Chao Wang, a construction management professor, and Fereydoun Aghazadeh, professor of industrial engineering, are working with Rutgers University as part of an integrated, multidisciplinary effort to bring emerging robotic technologies, such as a wearable exoskeleton, to the industrial construction industry.
As a preliminary step, the group is using a $150,000 National Science Foundation planning grant to perform a year-long pilot study and conduct virtual workshops to gather information from potential users.
It is all made possible by NSF’s 10 Big Ideas—Future of Work at the Human-Technology Frontier program and gives LSU and Rutgers one year to create a team of researchers to compete for a $3 million research grant this spring.
For now, the team is looking into how variable sensors and robotics technology can keep construction workers safe and increase their productivity. During the workshops, they’re also discussing the potential benefits of an exoskeleton device on health insurance costs and worker longevity.
“We want to listen to them and learn about their requirements on these projects,” Wang says, “as well as get their input and feedback.”
About 40 participated in the first workshop in December, a group comprised mostly of project managers from the construction industry in Louisiana and other states, as well as organizations such as Associated Builders and Contractors’ Pelican Chapter in Baton Rouge, Associated General Contractors of America and the National Institute for Occupational Safety and Health.
During the meetings, Wang and Aghazadeh are gathering information about potential challenges to implementing the exoskeleton in the field. A participant from Performance Contractors of Baton Rouge, for example, expressed concern that a metallic device might pose an electrocution risk, while others questioned the impact of dust and Gulf Coast humidity. All the information is helpful, Wang says. “We’re learning more about the practicality of its use in market and the industry.”
While LSU provides input from a contractor’s perspective, the Rutgers team helps with the technical design.
“We want the device to be smart enough to adjust to fit into various schemes,” Wang says. “We can also provide the real-world application once it gets to that stage.”
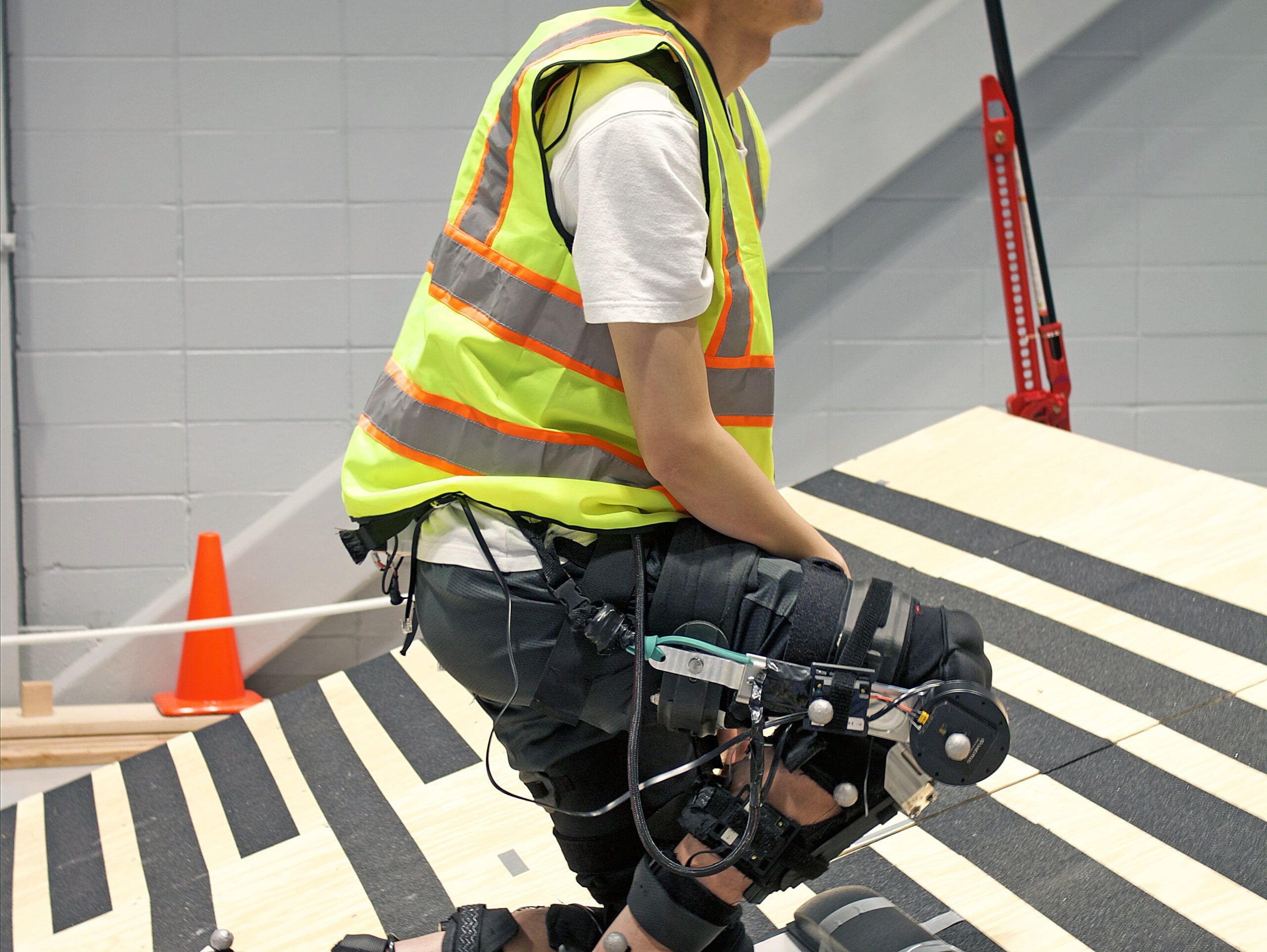
Science in Action
The main research grant application was due to the National Science Foundation in March and could eventually lead to the development and field testing of the exoskeleton should it be awarded to the LSU-Rutgers team. Chao expects the research phase to begin in October.
“It’s a three-year grant,” he adds. “We’re developing a prototype right now and we’ll eventually have two—one in New Jersey and one in Louisiana—for testing, feedback and improving the design.” The team will follow up with simulated constructed activities in the lab, then find industry partners for on-site field testing.
The collaborative research project is ahead of the game, as few, if any, construction companies have adopted exoskeleton technology.
The FW-HTF project has three primary objectives: develop lightweight, flexible, high-performance, personalized wearable exoskeletons for construction workers; develop machine learning-based human skill modeling and training in construction; and initiate new cross-disciplinary collaboration and foster engagement with industry partners and stakeholders.
“Construction workers get hurt for three reasons,” Aghazadeh says. “Number one, they are tired. Number two, the task is beyond their capacity. Number three, they are not properly trained. If they don’t have the capacity to do the physical work, how can we enhance their physical capability? We can give them more power.”
Wang, who serves as the project’s principal investigator, says there are a few exoskeleton products currently available on the market, but those mostly target an industrial manufacturing setting. The exoskeleton remains a novel concept in construction because the construction site is more dynamic and complicated.
“We’re seeing how we can explore personalized exoskeleton or robotics technology,” he adds. “In a manufacturing facility, a worker probably does the same thing 1,000 times a day. It’s repetitive, which is perfect for an exoskeleton because they design it just for that one task.
“A construction site is a lot different. You must be able to climb stairs, walk, squat, and reach out to different levels depending on what trade you are in. That makes it difficult to design an exoskeleton because you need something that can help with all these tasks. We are investigating how to make the exoskeleton smart enough to recognize what task the construction worker is doing and adjust its power level and control strategy to more effectively assist with the work.”
Wang and Aghazadeh will study which tasks each construction crew member performs to develop and train an exoskeleton that fits different construction tasks. In the process, they’ll consider if the robotic exoskeleton should support the upper or lower body and how much power should be given. “The robot must be smart enough to know what you’re trying to do and what your next move is,” Wang says, “so it can be adjusted accordingly.”